High tech installation for neoclassic building
The Concertgebouw is a unique concert hall with a long history. Looking for a way to upgrade the rigging installation, both the theatre consultant and the technical supervisor of the Concertgebouw turned to Controllux to source for a solution. Prolyte distributor Controllux involved ProLyft product manager Michiel van der Zijde to design and pitch for a customized hoist and control system for this unique, historical location. Based on their expertise and in-depth knowledge of the buildings requirements, the pitch involved long considerations with all engaged to come to a satisfying solution.
About the building
Built in 1888; The Concertgebouw in Amsterdam enjoys worldwide renown, both as residence to the Royal Concertgebouw Orchestra and due to its unrivalled acoustics. The building has a very dense performance programme, which covers up to 340 days a year. During every gap in the performance programme the Orchestra uses the auditorium for rehearsals.
In 1983 the building was classified as national monument, bringing restrictions to any renovation or technical update; visible changes are not allowed and any changes affecting the acoustics are strictly forbidden.
The monumental ceiling and rigging requirements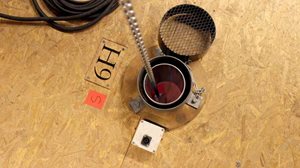
With only the nighttime available for set changes and technical building, rigging needs to be very efficient. This fact combined with the unique monumental and acoustic characteristics of the building required a very specific solution.
In the running up to this project, it became clear that the rigging installation needed to be efficient and operate as swift as possible, given the complexity of the installation.
The complete rigging installation had to be installed in the loft above the plastered ceiling. The ceiling sports a matrix of over 200 holes to allow hooks and chains to come through from the loft. This matrix is the only reference for the hoist operator to understand which hoists need to be selected. With the hoists being moved from hole to hole on a daily basis, a good reference solution was paramount to make the installation safe to operate.
The rigging requirements listed
Following the requirements from the technical team the installation needed to incorporate a range of technical features to make the rigging installation work within the limitations of the building. These included:
- A network of I-beams with trolleys on loft level making it possible to position the hoists easily above any hole in the ceiling.
- 4 lines of exchange positions to create the possibility to move trolleys with hoist from one I-beam to another and making it possible to pass hoists to position hoists in between other hoists.
- A control system that is not communicating to the operator in hoist numbers but in 208 ceiling hole numbers.
- 40 hoists rated for suspending over people, extendable to over 100 hoists.
- A load cell system on every hoist to be able to read the load and protect against overload.
- A height readout system on every hoist to be able to reposition trusses and, for example, line arrays after lowering for service. The height readout must also protect the system from touching the plastered ceiling.
- A wired and a wireless operator board.
Taking the solution to the next level – incorporating the Aetos range
In order to reach the requirements Controllux installed a network of I-beams, from which the hoists could run on trolleys and, together with Prolyte, installed an central, computerized, control system capable of controlling over 200 hoists.
In this system, each hoist is equipped with its own processor, an encoder and a load cell. Connecting these hoists to a central control with a power connector and a separate data line creates the opportunity for nearly unlimited control of the hoist position and load range it’s allowed to operate in.
When the hoists are positioned above a hole in the ceiling, a local control is used to lower the hook to a position just below the ceiling. A LED on the hoist will blink when the hook has reached its position. As a next step the local control, with a build in barcode reader, is used to scan the barcode that identifies the “hole”-position.
After scanning the barcode the hoist is enabled on the central control and selectable under the number of the hole. From then on the hoist operator has the choice to operate the hoists via either a touchscreen remote control or a wireless remote control.
The touchscreen remote is able to show the layout of the ceiling with the holes in the selection screen. In this mode individual hoists can be selected or (in this case) maximum 10 groups of hoists can be created. In the group mode, the screen can show detailed information per group of hoists, the availability of the hoists at the hole positions, loading per hoist and the position of the hook in millimeters. This being all very valuable and necessary information to be able to control the hoists with accuracy required to life up to the safety requirements. As an optional function, the screen is able to show the total load per roof beam.
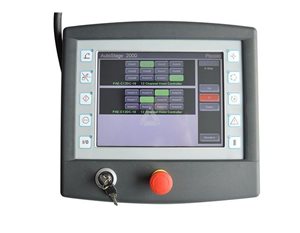
From the touchscreen remote groups of hoists can be allocated to the wireless remote. With the wireless remote you are able to move the (group of) hoists up and down. Safety is monitored by the central computer and made visible on the touchscreen remote. The emergency stop system operates at SIL3 level, and each E-stop is individually connected to the main computer, when an E-stop is pressed, this will show on the screen.
" For Prolyte this was a unique case to show and use all the features that the ProLyft Aetos system incorporates. It’s a pleasure to get a project that really requires all the control and monitoring possibilities the Aetos hoist and control systems can offer. The potential of the Aetos system is almost endless, which is clearly shown in this case” highlights Michiel van der Zijde from Prolyte."
Being able to offer a flexible, easy to control and sophisticated control system is why the combination of Controllux and Prolyte Group was favored over other suppliers.
With the installation concluded and the system in full operation, the Concertgebouw is really happy with the flexibility and operator safety the system has enabled. As Arnold van Duijn, Chief Operational Services, comments: ”Our experiences with this new system are really positive. Apart from the fact that work is now much easier, as we don’t have to lift and swap the hoists manually, also the patching and allocating of the hoists to the right hole position is really easy. We’re very content with the complete control system and all the options it offers, rigging and outlining line-array systems is now very fast and accurate, positions can be stored and repeated easily. Furthermore, the installing teams we’re a pleasure to work with, while most of the work needed to be done during the night, they showed great adaptability and remained flexible”.
Enrico Daamen of Controllux concludes: ”For a project on this scale, given the complexity of the installation we’re really satisfied with every aspect of it, from the first informative talks to the final implementation, Prolyte has proven its value as a knowledge partner throughout the entire process”.
Project details:
Customer:
Het Koninklijk Concertgebouw Amsterdam
Concertgebouwplein 10
1071 LN Amsterdam
Mr. T. Smit
Theatre Consultant:
Theateradvies bv
Herengracht 160
1016 BN Amsterdam
Mr. H. Huikeshoven
Prolyte Distributor:
Controllux BV
Tankval 5
2408 ZC Alphen aan den Rijn
Mr. Enrico Daamen